Budowa maszyn roboczych to złożony proces, który wymaga uwzględnienia wielu kluczowych elementów. Wśród nich można wyróżnić takie komponenty jak silniki, układy napędowe, ramy oraz systemy sterowania. Silniki są sercem maszyny, odpowiedzialnym za generowanie mocy potrzebnej do wykonywania różnych zadań. W zależności od przeznaczenia maszyny, mogą to być silniki elektryczne, spalinowe lub hydrauliczne. Układy napędowe natomiast przenoszą moc z silnika na inne elementy maszyny, co pozwala na jej ruch i wykonywanie pracy. Rama jest konstrukcją nośną, która musi być wystarczająco wytrzymała, aby utrzymać wszystkie pozostałe elementy oraz zapewnić stabilność podczas pracy. Systemy sterowania to z kolei mechanizmy, które umożliwiają operatorowi kontrolowanie funkcji maszyny, co jest niezwykle istotne w kontekście bezpieczeństwa i efektywności działania.
Jakie są najczęściej stosowane materiały w budowie maszyn roboczych
W budowie maszyn roboczych niezwykle istotny jest wybór odpowiednich materiałów, które zapewnią trwałość i efektywność działania urządzenia. Najczęściej stosowanymi materiałami są stal, aluminium oraz tworzywa sztuczne. Stal jest materiałem o wysokiej wytrzymałości i odporności na uszkodzenia mechaniczne, co czyni ją idealnym wyborem do produkcji ram i innych kluczowych elementów konstrukcyjnych. Aluminium z kolei charakteryzuje się niską wagą oraz dobrą odpornością na korozję, co sprawia, że jest często wykorzystywane w maszynach wymagających mobilności oraz w zastosowaniach przemysłowych. Tworzywa sztuczne, takie jak nylon czy poliwęglan, znajdują zastosowanie w elementach mniej obciążonych mechanicznie, ale wymagających odporności na działanie chemikaliów czy wysokich temperatur.
Jakie są najważniejsze zasady projektowania maszyn roboczych
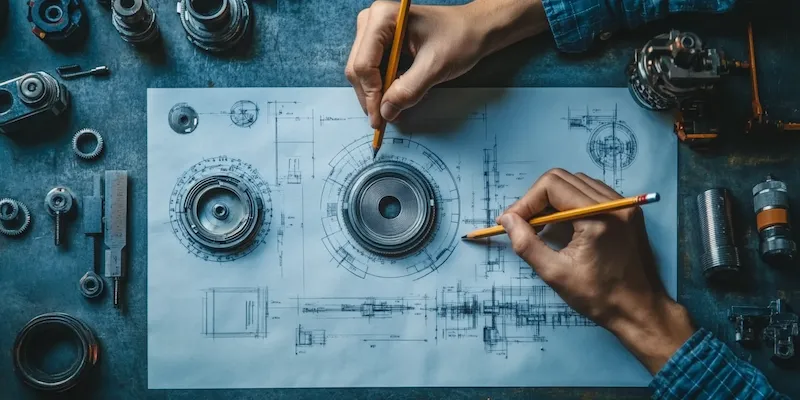
Projektowanie maszyn roboczych wymaga przestrzegania szeregu zasad inżynieryjnych oraz norm bezpieczeństwa. Kluczowym aspektem jest ergonomia, która ma na celu zapewnienie komfortu pracy operatora oraz minimalizację ryzyka urazów. Maszyna powinna być zaprojektowana w taki sposób, aby wszystkie jej elementy były łatwo dostępne dla użytkownika, a obsługa była intuicyjna. Kolejnym ważnym aspektem jest niezawodność konstrukcji; maszyny muszą działać bezawaryjnie przez długi czas nawet w trudnych warunkach eksploatacyjnych. Ważne jest również uwzględnienie aspektów ekologicznych; nowoczesne maszyny powinny być projektowane z myślą o minimalizacji wpływu na środowisko poprzez ograniczenie emisji szkodliwych substancji oraz zużycia energii. Również testowanie prototypów przed wdrożeniem do produkcji jest kluczowym etapem procesu projektowego; pozwala to na identyfikację ewentualnych problemów i ich korektę przed rozpoczęciem seryjnej produkcji.
Jakie są najnowsze technologie w budowie maszyn roboczych
W ostatnich latach nastąpił dynamiczny rozwój technologii związanych z budową maszyn roboczych, co znacząco wpłynęło na ich wydajność oraz funkcjonalność. Jednym z najważniejszych trendów jest automatyzacja procesów produkcyjnych; dzięki zastosowaniu robotów przemysłowych możliwe stało się zwiększenie precyzji oraz szybkości wykonywanych operacji. Również technologia druku 3D zaczyna odgrywać coraz większą rolę w produkcji komponentów maszyn; pozwala ona na szybkie prototypowanie oraz produkcję skomplikowanych kształtów bez konieczności korzystania z tradycyjnych metod obróbczych. Warto również zwrócić uwagę na rozwój systemów monitorowania i diagnostyki; nowoczesne maszyny są wyposażane w czujniki umożliwiające zbieranie danych o ich pracy w czasie rzeczywistym, co pozwala na szybką reakcję w przypadku awarii lub nieprawidłowości.
Jakie są przyszłe kierunki rozwoju budowy maszyn roboczych
Przyszłość budowy maszyn roboczych zapowiada się niezwykle interesująco dzięki ciągłemu postępowi technologicznemu oraz rosnącym wymaganiom rynku. Jednym z kluczowych kierunków rozwoju będzie dalsza automatyzacja procesów; coraz więcej przedsiębiorstw inwestuje w inteligentne systemy zarządzania produkcją oraz robotykę współpracującą, co pozwala na zwiększenie wydajności i elastyczności produkcji. W kontekście ochrony środowiska zauważalny będzie wzrost zainteresowania ekologicznymi rozwiązaniami; inżynierowie będą dążyć do projektowania maszyn o niższym zużyciu energii oraz mniejszym wpływie na środowisko naturalne. Ponadto rozwój technologii cyfrowych przyczyni się do powstania bardziej zaawansowanych systemów monitorowania i analizy danych; wykorzystanie sztucznej inteligencji w procesach diagnostycznych może znacząco poprawić niezawodność maszyn roboczych.
Jakie są kluczowe aspekty bezpieczeństwa w budowie maszyn roboczych
Bezpieczeństwo w budowie maszyn roboczych to jeden z najważniejszych aspektów, który należy brać pod uwagę na każdym etapie projektowania i produkcji. Kluczowym elementem jest przestrzeganie norm i standardów bezpieczeństwa, które regulują kwestie związane z konstrukcją oraz użytkowaniem maszyn. Wśród tych norm znajdują się m.in. dyrektywy Unii Europejskiej dotyczące maszyn, które określają wymagania dotyczące ochrony zdrowia i życia użytkowników. Ważnym krokiem jest również przeprowadzenie analizy ryzyka, która pozwala na identyfikację potencjalnych zagrożeń związanych z eksploatacją maszyny oraz opracowanie odpowiednich środków zaradczych. Kolejnym istotnym aspektem jest wyposażenie maszyn w systemy zabezpieczeń, takie jak osłony, czujniki czy automatyczne wyłączniki, które mają na celu minimalizację ryzyka wypadków. Szkolenie operatorów oraz personelu obsługującego maszyny również odgrywa kluczową rolę; pracownicy powinni być świadomi potencjalnych zagrożeń oraz umieć prawidłowo korzystać z urządzeń.
Jakie są wyzwania związane z modernizacją istniejących maszyn roboczych
Modernizacja istniejących maszyn roboczych to proces, który niesie ze sobą szereg wyzwań i trudności. Przede wszystkim, wiele starszych modeli maszyn zostało zaprojektowanych z myślą o technologiach sprzed kilku dekad, co może utrudniać ich dostosowanie do współczesnych standardów wydajności i efektywności energetycznej. Wymiana przestarzałych komponentów na nowoczesne rozwiązania często wiąże się z koniecznością przeprojektowania całej maszyny lub jej kluczowych elementów. Kolejnym wyzwaniem jest integracja nowych technologii, takich jak systemy automatyki czy czujniki monitorujące, z istniejącymi układami sterującymi; wymaga to zaawansowanej wiedzy inżynieryjnej oraz odpowiednich narzędzi diagnostycznych. Dodatkowo, modernizacja często wiąże się z przestojami w produkcji, co może generować dodatkowe koszty dla przedsiębiorstw. Warto także zwrócić uwagę na konieczność szkolenia personelu w zakresie obsługi nowoczesnych rozwiązań technologicznych; brak odpowiednich umiejętności może prowadzić do obniżenia efektywności pracy oraz zwiększenia ryzyka awarii.
Jakie są metody testowania i oceny wydajności maszyn roboczych
Testowanie i ocena wydajności maszyn roboczych to kluczowe etapy procesu produkcyjnego, które pozwalają na zapewnienie wysokiej jakości i niezawodności urządzeń. Istnieje wiele metod testowania, które mogą być stosowane w zależności od rodzaju maszyny oraz jej przeznaczenia. Jedną z najpopularniejszych metod jest testowanie funkcjonalne, które polega na sprawdzeniu wszystkich funkcji maszyny w warunkach rzeczywistych. Ważnym aspektem jest również testowanie obciążeniowe; polega ono na symulacji warunków pracy maszyny przy maksymalnym obciążeniu, co pozwala na ocenę jej wydajności oraz identyfikację ewentualnych słabości konstrukcyjnych. Kolejną metodą jest analiza drgań, która umożliwia wykrycie nieprawidłowości w działaniu mechanizmów oraz ocenę stanu technicznego maszyny. Testy powinny być przeprowadzane zgodnie z obowiązującymi normami oraz procedurami, aby zapewnić rzetelność wyników. Po zakończeniu testów ważne jest sporządzenie raportu zawierającego wyniki oraz rekomendacje dotyczące ewentualnych poprawek lub modyfikacji konstrukcyjnych.
Jakie są różnice między maszynami roboczymi a innymi rodzajami sprzętu
Maszyny robocze różnią się od innych rodzajów sprzętu przede wszystkim swoim przeznaczeniem oraz sposobem działania. Głównym celem maszyn roboczych jest wykonywanie określonych zadań przemysłowych lub budowlanych, takich jak cięcie, spawanie czy transport materiałów. W przeciwieństwie do urządzeń konsumpcyjnych czy biurowych, maszyny robocze są projektowane z myślą o intensywnej eksploatacji w trudnych warunkach pracy. Kolejną istotną różnicą jest ich konstrukcja; maszyny robocze często składają się z bardziej skomplikowanych układów mechanicznych oraz elektronicznych niż inne rodzaje sprzętu, co wpływa na ich cenę oraz wymagania serwisowe. Dodatkowo, maszyny robocze muszą spełniać rygorystyczne normy bezpieczeństwa oraz efektywności energetycznej; ich projektowanie wymaga zaawansowanej wiedzy inżynieryjnej oraz znajomości specyfiki branży. Warto także zauważyć, że maszyny robocze często wymagają specjalistycznego szkolenia dla operatorów; ich obsługa wiąże się z większym ryzykiem niż korzystanie z prostych urządzeń codziennego użytku.
Jakie są zastosowania maszyn roboczych w różnych branżach
Maszyny robocze znajdują szerokie zastosowanie w różnych branżach przemysłowych i usługowych, co czyni je niezbędnym elementem współczesnej gospodarki. W sektorze budowlanym wykorzystuje się je do wykonywania prac ziemnych, takich jak kopanie fundamentów czy transport materiałów budowlanych; przykładem mogą być koparki czy ładowarki. W przemyśle produkcyjnym maszyny robocze są wykorzystywane do montażu komponentów, obróbki metali czy pakowania produktów; tu szczególnie popularne są roboty przemysłowe oraz linie montażowe. Również w logistyce i magazynowaniu maszyny odgrywają kluczową rolę; wózki widłowe i systemy transportu wewnętrznego umożliwiają efektywne zarządzanie przepływem towarów. W branży rolniczej maszyny rolnicze takie jak traktory czy kombajny znacznie zwiększają wydajność prac polowych i zbiorów.
Jakie są przyszłe trendy w rozwoju technologii budowy maszyn roboczych
Przyszłość technologii budowy maszyn roboczych zapowiada się dynamicznie dzięki postępom w dziedzinie automatyki, robotyki oraz sztucznej inteligencji. Jednym z głównych trendów będzie dalsza automatyzacja procesów produkcyjnych; coraz więcej firm inwestuje w inteligentne systemy zarządzania produkcją oraz robotykę współpracującą, co pozwala na zwiększenie wydajności i elastyczności produkcji. Również rozwój Internetu Rzeczy (IoT) wpłynie na sposób monitorowania i zarządzania maszynami; dzięki połączeniu urządzeń z siecią możliwe będzie zbieranie danych o ich pracy w czasie rzeczywistym oraz optymalizacja procesów eksploatacyjnych. Zwiększone zainteresowanie ekologicznymi rozwiązaniami sprawi natomiast, że inżynierowie będą dążyć do projektowania maszyn o niższym zużyciu energii oraz mniejszym wpływie na środowisko naturalne poprzez zastosowanie materiałów biodegradowalnych czy odnawialnych źródeł energii.